Roof construction safety breakthrough at Rotherham’s AMRC
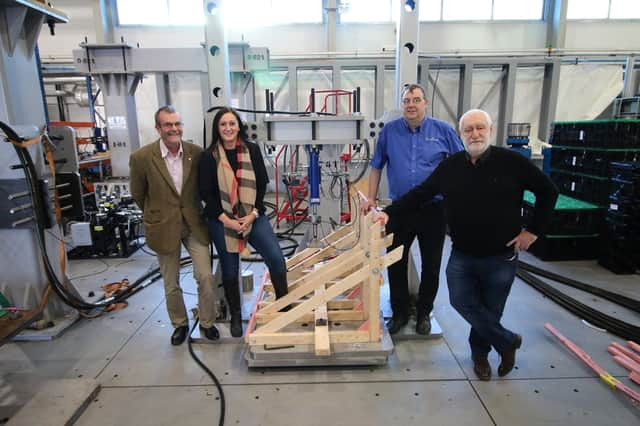
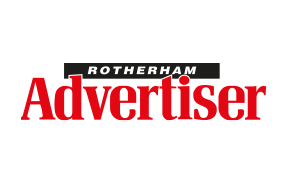
The new joints created by Keah director Ken Johnson (70) have been tested and verified for use at Rotherham’s Advanced Manufacturing Research Centre.
The AMRC’s Advanced Structural Testing Centre put the product through its paces and it is now ready to go into production.
Advertisement
Hide AdAdvertisement
Hide AdMr Johnson, from Leeds, set up Keah after he retired from construction to use his experience to improve building processes.
He said: “I thought there must be a smarter way to complete those time-consuming intensive manual jobs.
"The roof batten joint can join two roof battens at any point on the roof which will save time and material waste.
“The testing is invaluable as it means we will now be able to confidently state the load bearing weights of our product and the joints are ready to go into production thanks to the AMRC.”
Advertisement
Hide AdAdvertisement
Hide AdPhil Spiers, head of the AMRC testing centre, said: “Our tests have so far shown that the joints are stronger than traditional nailed roof batten fixtures and experience lower rates of failure.
“We have validated that the optimum load weight for use is 20st, but the joints can support all the way up to 50st in weight."
"The idea for the product itself is beautifully simple, but it is a powerful concept that will make a laborious task safer.”
Keah benefited from a grant from the High Value Manufacturing Catapult to cover 50 per cent of the testing costs.
Mr Johnson said: “For a small company such as ours, it really helps us get this pioneering roofing product off the ground.”